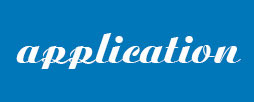

Maximize the heat recovery and minimize the pollution impact Metallurgical industry is an important raw material industry sector, known as the "industrial food," said, usually divided into ferrous metallurgy industry and non-ferrous metallurgy industry two categories. The iron and steel industry is the main body of the ferrous metallurgy industry, mainly including the iron making, steel making and the coal chemical industry. Non-ferrous metallurgy, including copper, aluminum, lead, zinc, nickel, gold and other metals processing and smelting. The level of development of metallurgical industry is an important symbol of a country's comprehensive national strength, which is closely related to people's lives. The development of metallurgical industry will bring a serious threat to the environment and energy, including flue gas pollution and emission pollution and high energy consumption. For heat recovery and recycling of products emissions, will provide a reliable guarantee for the healthy development of the metallurgical industry, and can realize energy saving and emission reduction to achieve the sustainable development of metallurgical industry. Dragon company is enterprises to provide all kinds of process heat transfer products and services from the detachable heat exchanger to semi welded plate heat exchanger to the welded wide channel of plate heat exchanger, heat recovery system, widely used in the cooling system, including acid system, alumina process heat utilization and electrolyte cooling etc., and actively committed to energy saving products and system development of the metallurgical industry in high and low temperature heat energy recovery system, coking by-product recovery system, and provides system solutions for users of energy saving and emission reduction, create considerable benefits for the user. The heat transfer products and systems required for metallurgical industry the use of complex media, product type involves many, dragon always for users in the choice of materials, to provide the best solutions in terms of anticorrosion design and structure design, implementation of operating system intensive, when you choose the Dragon Teng, if you only want to harvest a wisp of spring breeze dragon, will give you the entire spring! iron and steel smelting In the steel smelting process, we provide professional services in a number of processes: 1 blast furnace closed water cooler 2 closed water cooler for electric arc furnace 3 oxygen lance, oxygen lance cooler 4 continuous casting crystallizer water cooler 5 cold rolling oil cooler nonferrous metal The production methods of alumina can be roughly divided into four kinds: alkali, acid, acid and alkali, heat. The alkaline method is divided into Bayer process, sintering process and Bayer sinter combination method. Alkali is treated with alkali aluminum ore, Alumina ore transformation into sodium aluminate solution, such as iron and titanium impurities in the ore and most of the silicon become insoluble compounds, insoluble residue (red mud) and solution separation, after washing and recovery of useful components herein, precipitation of aluminum hydroxide decomposition the pure sodium aluminate solution, and liquor separation, roasting after washing, alumina products. The application of plate heat exchanger in the alumina industry is mainly the cooling of the cooling water in the decomposition section, which is cooled to the temperature of the process by the gradual cooling (respectively with the mother liquor and water heat exchange). Because the semen (supersaturated sodium aluminate solution) to "scarring", the need for regular cleaning of a plate heat exchanger, cleaning liquid to strong alkaline or acid. Sheet material can choose 316L, 254SMo, AL-6XN, etc.. The utility model relates to a full welded wide channel plate heat exchanger which is applied to the middle cooling section of the decomposition and classification process in the production process of alumina, and is installed on the top of the decomposing tank to reduce the temperature of the aluminum hydroxide slurry during the decomposition process. Its main features are as follows: 1 wide channel side operation medium for aluminum hydroxide slurry, medium flow rate is generally 0.6 ~ 1.2m/s. High flow rate of the fluid containing solid particles on the surface of the plate flow, without accumulation or scarring blockage. 2 the width of the channel side without contact, the fluid can be completely free flow, and is full of the entire flow path formed by the plate, the plate surface is almost all involved in the heat exchange, in the flow channel to achieve no "dead zone" flow. 3 the slurry inlet and outlet parts are provided with a distribution structure, and the slurry is first passed through the distribution port and then into the distribution box, and finally enters into each wide channel uniformly. 4 the side distribution box and the cooling water side tube box adopt the detachable structure of flat cover plate. Between the 5 plates on the use of a very good form of ball welded structure, the pressure bearing capacity. 6 plate material selection SAF2205 (S31803) dual phase steel, is a good solution to corrosion and abrasion. The form of the 7 plate beam is horizontal, the slurry is put into the upper and lower, and the sedimentation and the scab of the slurry can be effectively suppressed. |